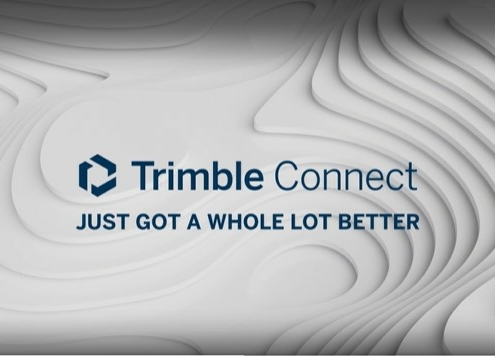
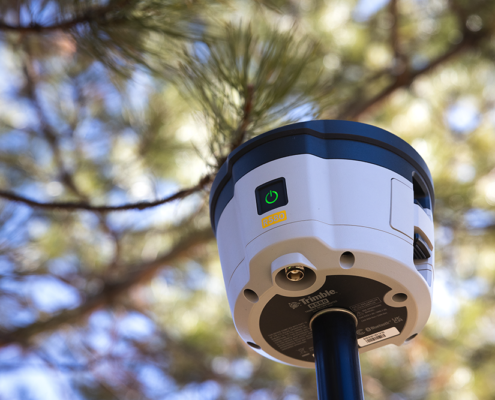
R580 GNSS Smart Antenna
ProductThe Trimble R580 GNSS Smart Antenna. Affordable, precise GNSS for efficient surveying and construction projects. Call 1800 748 324.
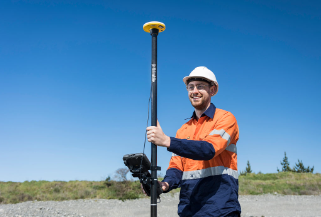
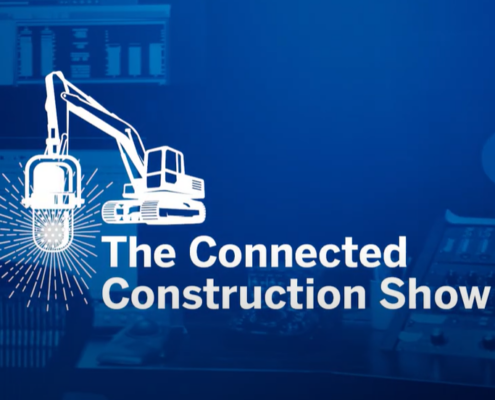
Roll on! Autonomy’s progress in highway construction
Product, TechnologyRoll on! Autonomy’s progress in highway construction. Trimble has introduced the Trimble® Siteworks Machine Guidance Module.
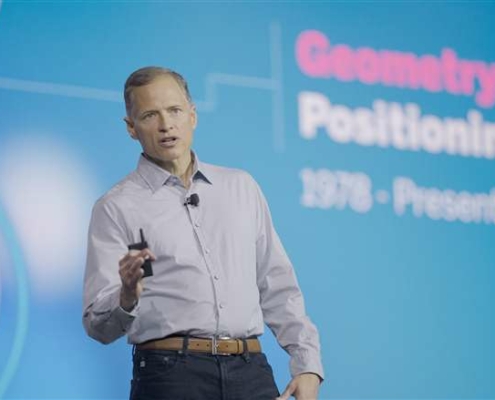
CONSTRUCTION TECHNOLOGY TRENDS
News, Product, TechnologyConstruction Technology Trends. Now that we’re settling back into the grind of work, let’s take a look at the technology trends to watch.