Tag Archive for: Trimble
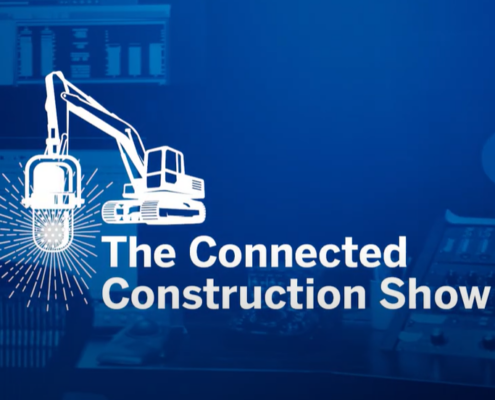
Roll on! Autonomy’s progress in highway construction
Product, TechnologyRoll on! Autonomy’s progress in highway construction. Trimble has introduced the Trimble® Siteworks Machine Guidance Module.
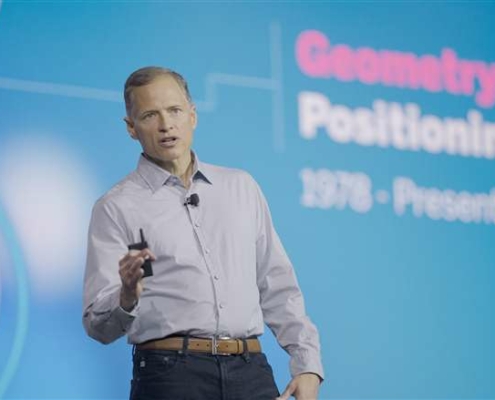
CONSTRUCTION TECHNOLOGY TRENDS
News, Product, TechnologyConstruction Technology Trends. Now that we’re settling back into the grind of work, let’s take a look at the technology trends to watch.
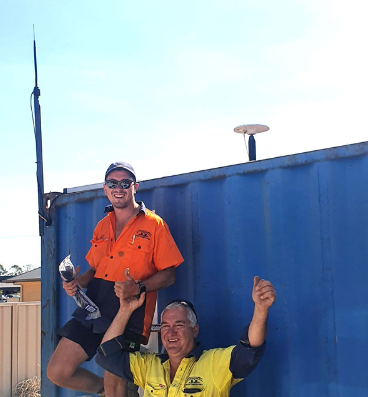
Technology Partnership Puts Earthmoving Company on Operational Solid Ground
News, Product, Technology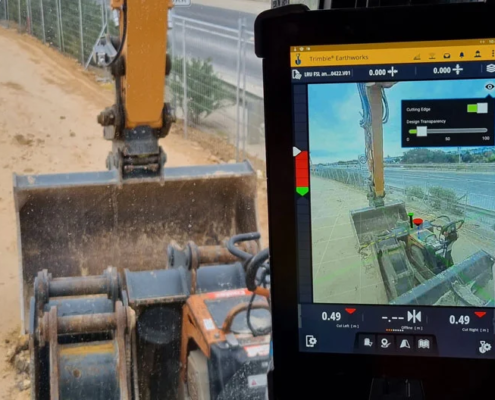
The Practical and Purposeful Application of Augmented Reality from a Contractor’s Perspective
Case Studies, News, Product, SiteVision, Technology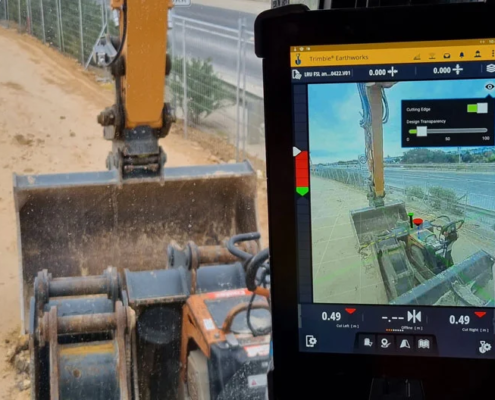
Training Leader Looks to Fill the Technology Gap on Heavy Equipment
News, Partnership, Technology[siteorigin_widget class="SiteOrigin_Widget_Image_Widget"][/siteorigin_widget]
As a company that prides itself on adapting to the needs of students and employers, Major Training Group, one of Australia’s oldest registered training organisations,…