Tag Archive for: UPG
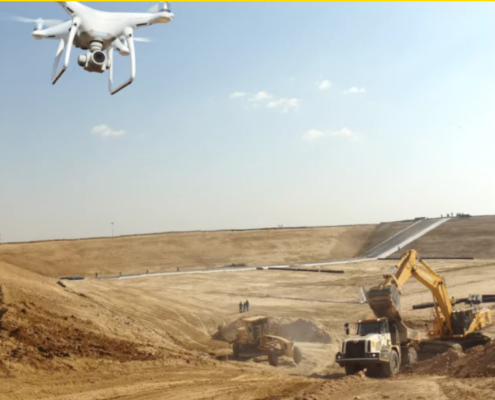
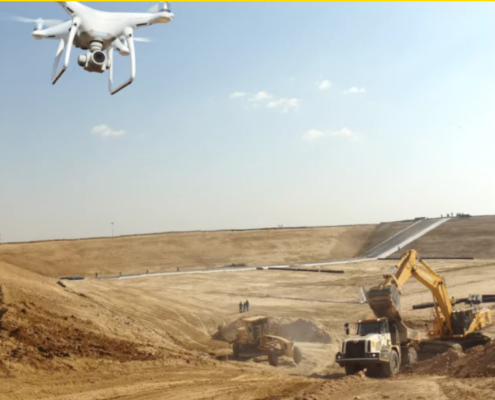
TerrusM – Fast Mobile Mapping
Technology
After recognising a gap in the marketplace for large scale maps, UPG, part of the SITECH Construction Systems Group, has become an authorised distributor of TerrusM, a lightweight, portable mobile scanner that rapidly documents and manages…
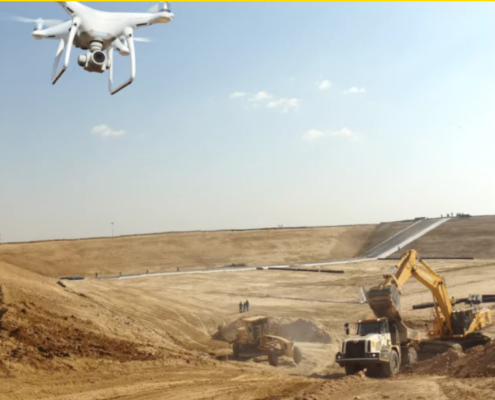
New Trimble® X7 plays its part in Scanning History
Product, Technology[siteorigin_widget class="SiteOrigin_Widget_Hero_Widget"][/siteorigin_widget]
Ever since the Trimble® X7 was introduced into the market in Australia, MinStaff Survey has been eager to get hold of one, and that became a reality recently when…
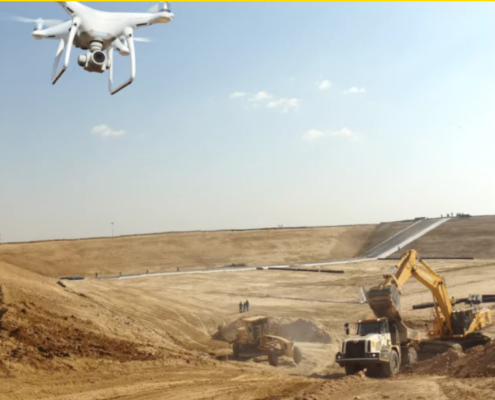
SITECH and UPG double up to get council operations on grade
Product, Technology
SITECH’s Dillon Harding and UPG’s Josh Weckert have teamed up to provide the total solution for a rural council.
The pair delivered and installed GCS900 Grade Control on a Wentworth Shire Council grader, a Cat® 140M, and also delivered…
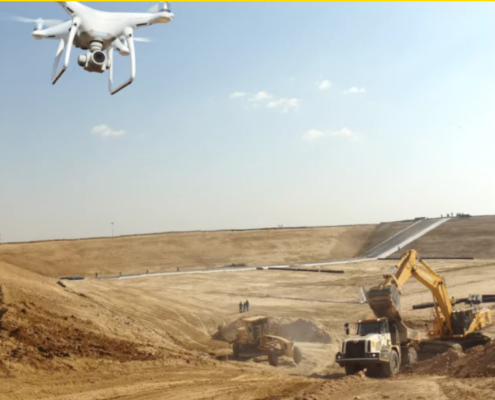
SITECH puts Trimble experience in operators’ hands
Construction, Product, Technology
Technology that is changing the face of construction went on show and customers got their feet dirty at a special open day near Adelaide.
SITECH Construction Systems, the official distributor for Trimble products, teamed with earthmoving…