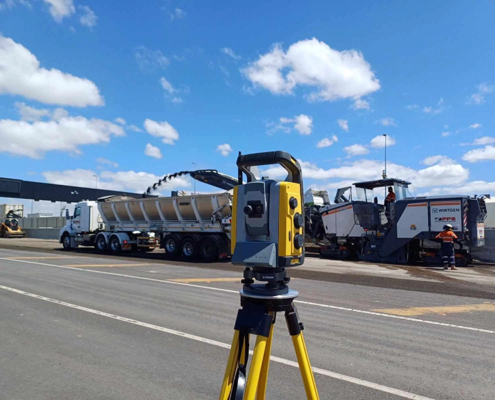
Award-winning results for Patten Pavement Services with Trimble UTS
Customer Story, NewsPatten Pavement Services and SITECH Construction Systems working to achieve award-winning results with Trimble UTS.
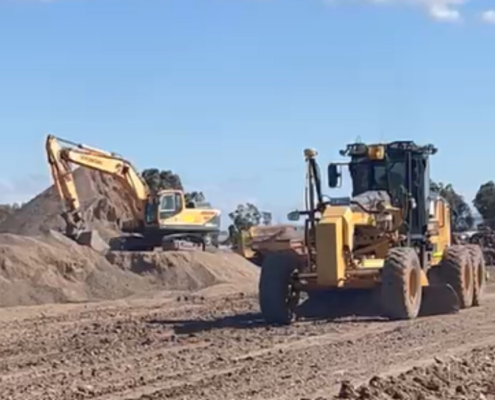
Teamwork Triumph: Grader back on track in under 24 hours
Customer Story, NewsPavilion Farms, SITECH and Contour Geoconstruction collaborate to get a critical grader operational in under 24 hours.
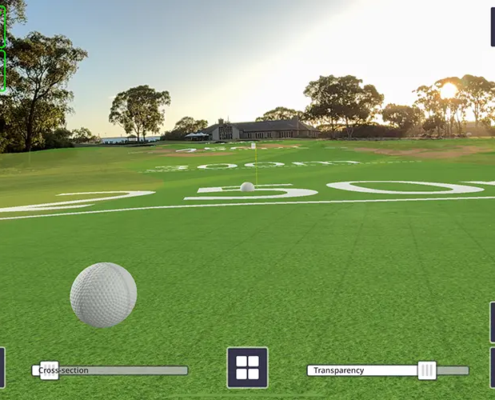
Trimble Workflow Solutions for a Winning Drive
General Information, NewsTrimble Workflow Solutions helped SITECH seamlessly integrate technology, enhancing collaboration and performance at the CCF Golf Day.
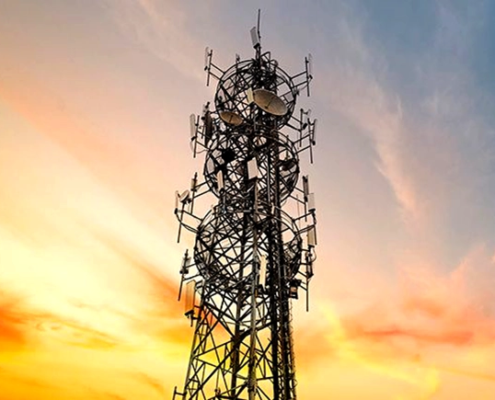
3G Network Closure
General Information, News, Version Update
The closure of the 3G network in Australia will affect older equipment. Upgrade to 4G to ensure continued functionality of your devices.
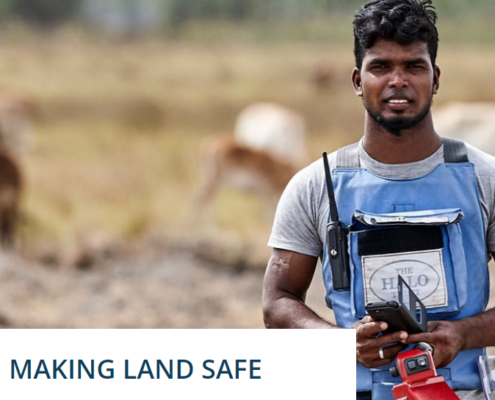