Tag Archive for: Drones
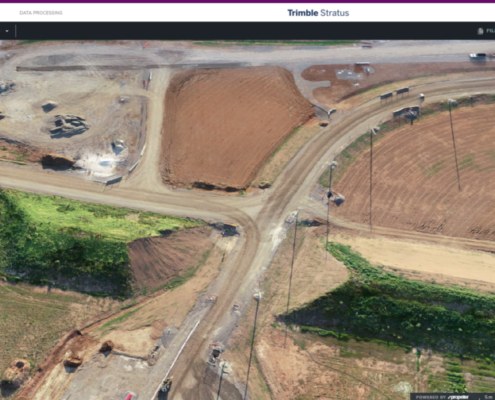
Expanding Possibilities: Technologies that Span the Design-through-Construction Lifecycle
Construction, SiteVision, Software, TechnologyExpanding Possibilities: Technologies that Span the Design-through-Construction Lifecycle. Familiar technologies that are helping.
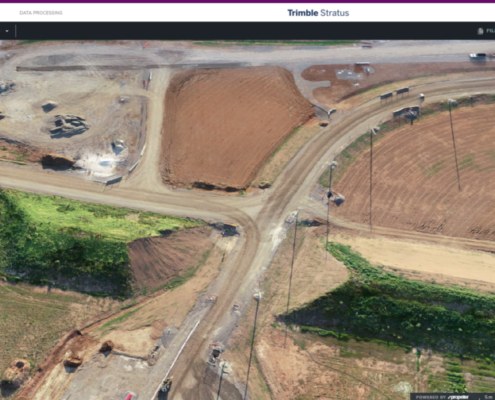
SEE Civil takes flight with Trimble, SITECH and Propeller
Construction, Product
When SEE Civil wanted to advance its unmanned aerial vehicle (UAV) survey drone program, they turned to Trimble, Propeller and SITECH Construction Systems.
SEE Civil has more than 30 years of experience completing a wide variety of projects…